About us
Corporate History
History of company
Karoku Mine started business as a sole proprietor at Fukagawa, Tokyo. He manufactured mechanical rail signal products and installed them on-site.
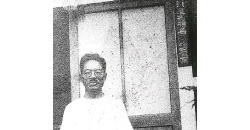
Nameplate at the time of establishment and the first President Karoku Mine
Mine-type Lever Force Reducer(pneumatic system) was first installed at Osaki West Signal Cabin.
MI-NE SEISAKU-SHO GSK was founded as a limited partnership company.
Appointed as a designated manufacturer and constructor by the Ministry of Railway.
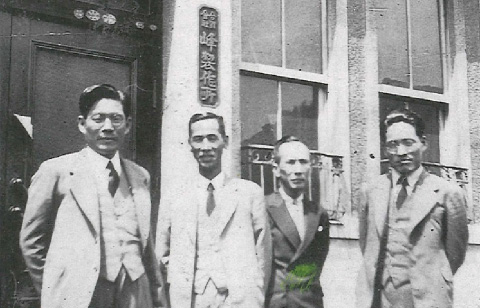
Nameplate of MI-NE SEISAKU-SHO Limited Partnership Company
The number of installed Mine-type Lever Force Reducer reached 300 sets.
Shade for railway signal light were installed nationwide as air defense measures.
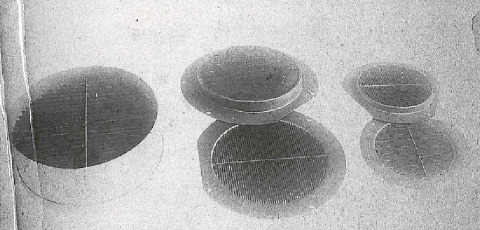
Shade for railway signal light
Mechanical Signal Installation Department was transferred to Railroad Maintenance Industry Co., Ltd., as a part of national policy in wartime.
Main office and plant in Fukagawa Tokyo completely destroyed by Bombing of Tokyo (Tokyo great air raid).
We evacuated to Kafuri, Maebaru-cho, Itoshima-gun, Fukuoka-ken to reconstruct the plant.
Head office was transferred to Tsukiji, Chuo-ku, Tokyo.
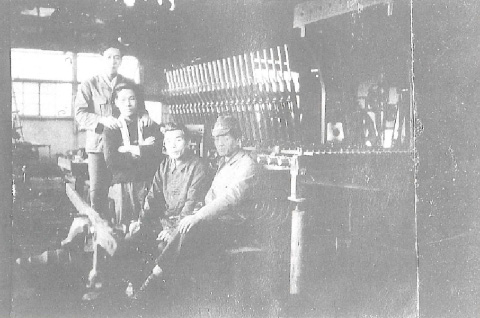
Assembly area of Production Section in Kafuri Plant
Karoku Mine founded MI-NE SEISAKU-SHO CO., LTD. capitalized at one million Japanese Yen, and became the first president.
Head office was transferred to Kanda, Chiyoda-ku, Tokyo.
We started manufacturing and sales of turnouts taking the opportunity of the implementation of the disclosed competitive bid system of Japanese National Railways.
Mechanical Signal Installation Department was revived.
We successfully performed the trial operation of a prototype of an on-board switching device (Type M1) on Makiyama Main Track in Yahata Steel Works.
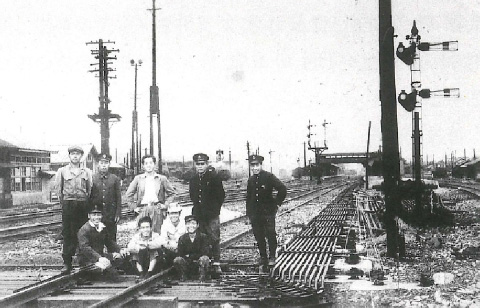
Restoration work for East Signal Cabin of Haiki Station
Research of Thermit welding was started.
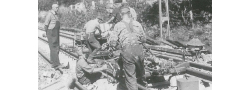
Field-work for Thermit rail welding
Kyushu Plant was built at Koga, Kasuya, Fukuoka (Now Koga city in Fukuoka) and production was transferred.
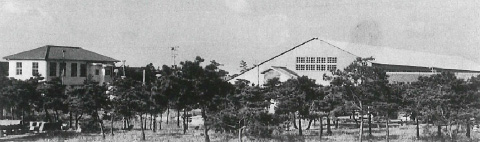
New plant in pine forest
Mine’s original Thermit rail welding method (MT1) was completed.
Mechanical Signal Installation Department was separated again upon the request of Japan National Railways and Showa Kogyo Co., Ltd., was established.
Construction department(current Yahata Branch Office) was established to dedicate installation and maintenance of on-board turnout switching system.
Thermit welding method was substantially applied to the conventional railroad line.
Osaka Branch Office (current Osaka Sales Branch Office) was established.
MI-NE engaged in welding work on the Tokaido Shinkansen construction site by Thermit welding method (MT2).
Supplied turnouts and expansion joints to Shinkansen (50T rail).
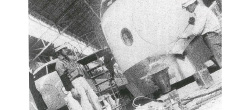
Brief sketch of Thermit welding for Tokaido Shinkansen
Capital was increased to 50 million yen.
Kimitsu Field Office (current Kimitsu Branch Office) was established at Kimitsu Steel Works.
Enclosed arc rail welding and gas pressure rail welding (RGP) for Sanyo Shinkansen (Shin-Osaka to Okayama) were started.
Mine Building was completed in front of Hakata Station.
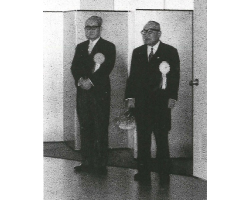
President Karoku Mine (right) and Vice President Kan-ichi Mine (left) in completion ceremony
Turnouts (for 60K rail) for Shinkansen were delivered to Sanyo Shinkansen (Okayama to Hakata).
Thermit rail welding (MTN) was performed.
Kan-ichi Mine became the second president.
Capital was increased to a hundred million Japanese yen.
MI-NE formed a technical alliance with Elektro-Thermit (Germany) with regard to Thermit welding (SkV method). The method was named Goldsummit welding, and sales of materials and welding service were started.
Turnouts (for slab) for Shinkansen were delivered to Tohoku Shinkansen (Omiya to Morioka) and Joetsu Shinkansen (Omiya to Niigata) and rail welding was performed.
Signal products were delivered to Baoshan Iron & Steel Co., Ltd., in China (206 sets).
MI-NE engaged rail welding at Seikan Tunnel.
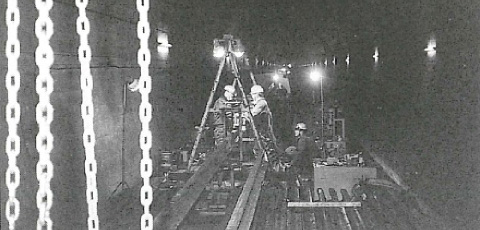
Rail gas pressure welding in Seikan Tunnel

Rail gas pressure welding in Seikan Tunnel
Development of pressure-welded crossing was accomplished. It was installed at Kokura Station of Kagoshima Main Line and Nippo Main Line for testing.
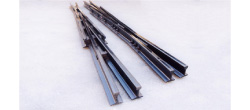
Pressure-welded crossing
Nagoya Branch Business Office (current Nagoya Branch) was established.
MI-NE manufactured expansion equipment for buffer girders for Honshu-Shikoku Bridge, installed it on-site, and engaged rail welding.
Rail Tension Gas Pressure Welding method was established. Construction was started.
Engineering guidance for enclosed arc welding was provided to Indonesia National Railways.
Three-rail turnouts (for pressure-welded crossings) were delivered to Yamagata Shinkansen, and rail welding was performed.
Hidetaka Mine became the third president.
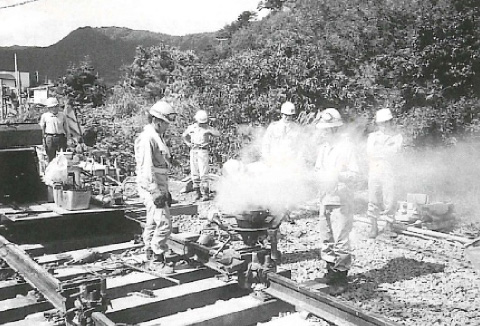
Rail welding for Yamagata Shinkansen
Technical R&D Lab. was established and memorial symposium was held. (Theme: "New railroad technology prospecting the 21st century").
Movable nose crossing (Rail steel-made pressure-welded nose specification) was developed and installed at Katata Station of Kosei Line.
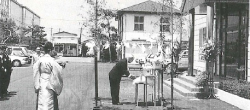
Opening ceremony for Technical R&D Lab.
Special turnout device for mobile launcher platform was supplied to the Tanegashima Space Center.
Welding of 100kg rail was performed.
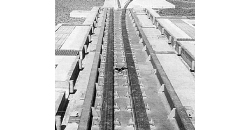
Special turnout device
Upon the 70th anniversary of the company establishment, the Lecture Hall was completed in Kyushu Plant.
Three-rail turnouts were delivered to Akita Shinkansen construction-site.
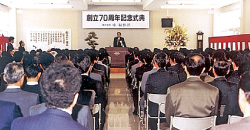
Ceremony for the 70th anniversary of the company establishment
Rail welding was performed on the Hokuriku Shinkansen (Takasaki to Nagano) construction site. Gas pressure welding of 80S tongue rail (42 m in length, longest in Japan) for the 1 in 38 turnout was first performed.
The Koga Satellite Office of the Fukuoka Branch Office (current Fukuoka Sales Branch Office) was established, and sales of welfare products were started.
Supply of Steel Sleeper Turnout was accelerated.
Movable Wing Crossing (noise reduced crossing) was developed and installed at Hakata operation department.
Upon the 75th anniversary of the company establishment, the Kyushu Plant Main Building was completed.
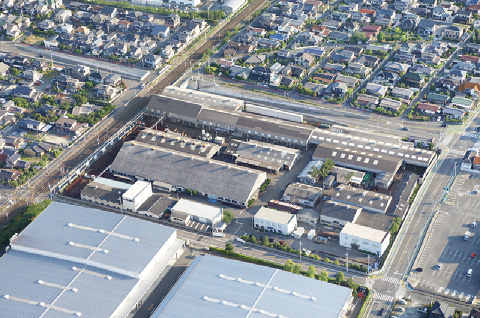
Kyushu Plant
Rail welding was performed on the Tohoku Shinkansen (Morioka to Hachinohe) construction site.
Movable wing crossings (noise reduced crossings) were delivered to the Koishikawa Depot of Tokyo Metro and installed.
Kyushu plant was certified to ISO9002.
Turnouts for the Shinkansen were delivered to the Kyushu Shinkansen (Shin-Yatsushiro to Kagoshima Chuo) construction site, and rail welding was performed.
Osaka Construction Office of the Osaka Branch Office was transferred to Otori. (Current Osaka Construction Office and Osaka Construction Branch Office)
Movable nose crossings (rail steel-made pressure-welded nose specification) were delivered to Tokyu Railways.
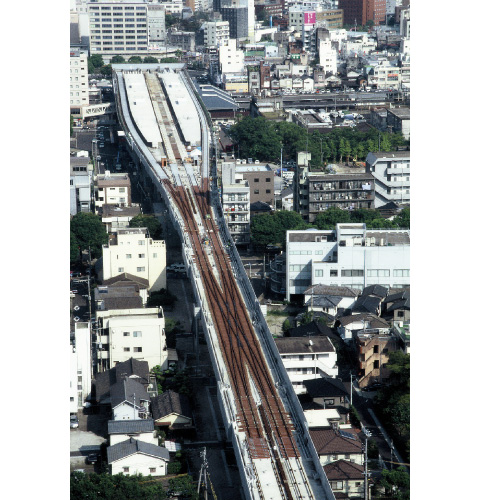
Kagoshima Chuo station
Since we switched to ISO9001: Version 2000, the application was expanded to sales, welding, engineering and research departments.
Welding Training Center was founded.
Crossovers for construction were delivered to the Taiwan Shinkansen. (26 sets)
Engineering guidance for gas pressure welding was provided to Vietnam National Railways.
Signal products were delivered to Baoshan Iron & Steel Co., Ltd., in China. (82 sets)
Upon the 80th anniversary of the company establishment, the Welding Main Building (current Fukuoka Construction Branch) was completed.
LRT turnouts were delivered to the Kumamoto City Transportation Bureau.
Akita Construction Office was established.
Main Office was transferred to Kanda-Kajicho, Chiyoda-ku, Tokyo.
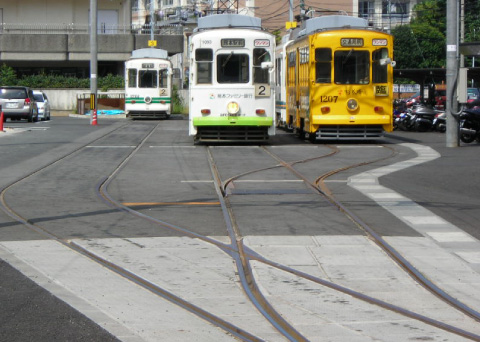
LRT
Turnouts for the Shinkansen were delivered to the Kyushu Shinkansen (Hakata to Shin-Yatsushiro) construction site, and rail welding was performed.
Rail welding was performed on the Tohoku Shinkansen (Hachinohe to Shin-Aomori) and the Hokkaido Shinkansen (Shin-Aomori to Shin-Hakodate Hokuto) construction sites.
Toshiaki Mine became the fourth president.
Rail build up welding for LRT rails was performed for the Kumamoto City Transportation Bureau.
Semi-automatic enclosed arc welding was performed on the Hokkaido Shinkansen (Seikan Tunnel) construction site.
Rail welding was performed on the Hokuriku Shinkansen (Nagano to Kanazawa) construction site.
New type movable nose crossing was exhibited in the 1st Mass-Trans Innovation Exhibition.
Rail welding was performed as remedial work for the Great East Japan Earthquake.
Rail products were delivered to Vietnam National Railways.
We participated in the 2nd Mass-Trans Innovation to demonstrate Goldsummit welding and exhibit a model of new type movable nose crossing.

LRT rail build up welding
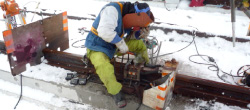
Rail welding for Hokuriku Shinkansen
Total 1,000 sets of steel sleeper turnout were delivered.
The Tokyo Construction Office of the Tokyo Construction Branch Office was established.
Three-rail turnouts were delivered to the Hokkaido Shinkansen construction site.
We participated in the 3rd Mass-Trans Innovation Exhibition to demonstrate Goldsummit welding and exhibit the point section of embedding type turnout and the embedding type point machine.
Total 10,000 sets of pressure welded crossing were delivered.
Turnouts were delivered to the 4th blast furnace repair site of Tobata at the Yahata Steel Works of Nippon Steel Corporation.
THR test was performed in Kagoshima Main Line and Nippo Main Line first in Japan.
New type movable nose crossing was experimentally installed in Takatori Station of Sanyo Line.
The 90th anniversary ceremony was held.
We participated in the 4th Mass-Trans Innovation Exhibition to demonstrate THR welding (Thermit Head Repair method) and exhibit a new type of movable nose crossing.
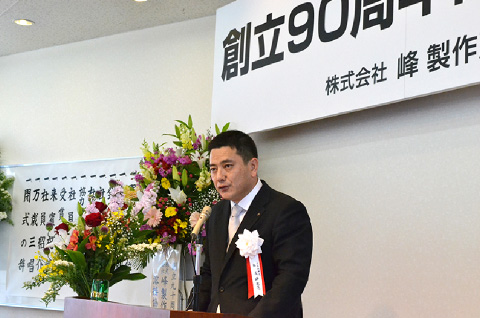
The 90th anniversary ceremony
Pressure welded crossings for EN54 rails were delivered to Indonesia.
The Akita Construction Office was transferred to Nakadori, Akita City.
We participated in the 5th Mass-Trans Innovation Exhibition to exhibit pressure welded crossing, one of our major products.
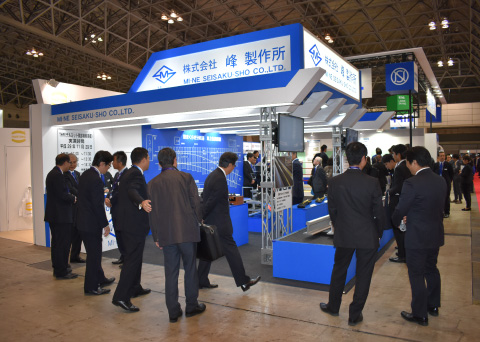
The 5th Mass-Trans Innovation Exhibition
Rail welding was performed on the Kyushu Shinkansen (Takeo Onsen to Nagasaki) construction site.
Nagoya Branch Business Office was reorganized to the Branch Office and transferred to Ichinomiya City, Aichi Prefecture.
Turnouts for JIS rail were delivered to Myanmar.
We participated in the 6th Mass-Trans Innovation to demonstrate Goldsummit welding and exhibit pressure-welded crossing.
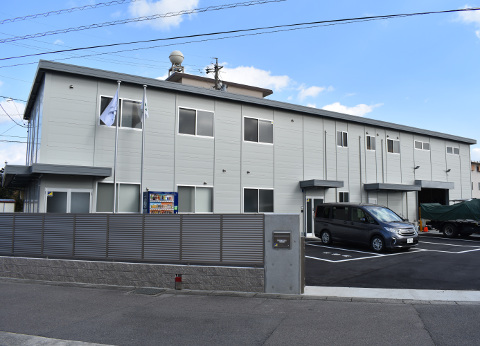
Nagoya Branch